How to Choose the Best CNC Router Machines for Beginners in 2021?
Mike Posted on June 09, 2021
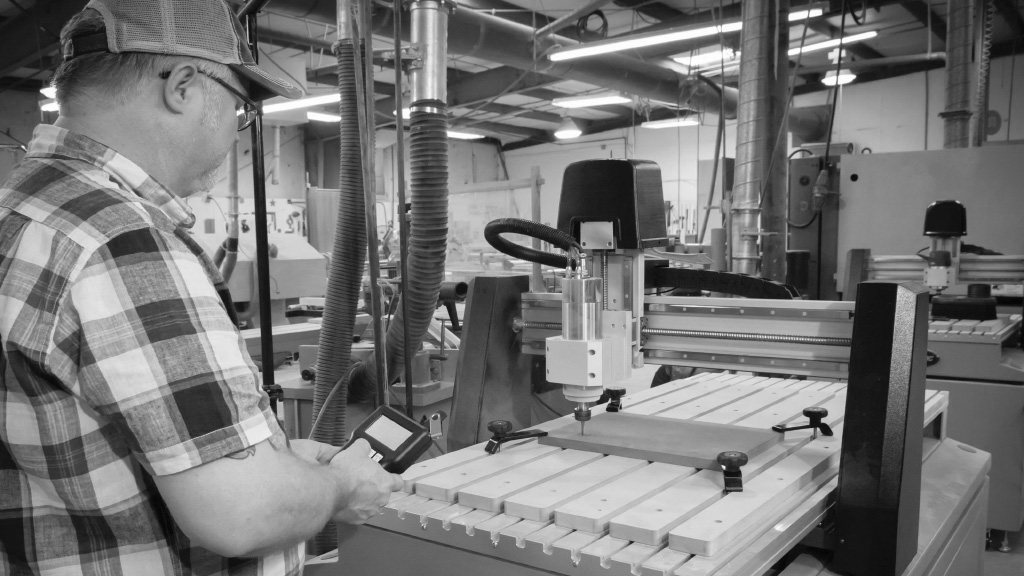
Are you looking for a CNC router machine to start your business? Review the practical guide to CNC routers for beginners in 2021. Make your CNC router table plans for your projects & ideas.
Definition
CNC router is an intelligent machine tool that automatically calculates the tool path through the computer to carve the designed pattern on the object. A CNC router machine accepts instructions from the computer, controls the linear linkage between the X, Y, and Z axes, and drives a router bit on the spindle to move along the tool path on the material to obtain the desired effects of engraving or cutting.
Concept
Workbench
The sheet metal with T-slots on the upper surface of the CNC router table is used as a workbench for fixing the workpiece. The surface flatness of the worktable and the parallelism with the feed axis have high requirements, and it is forbidden to cut the worktable with tools.
Spindle
The main shaft is a cylindrical motor above the CNC router table. The spindle drives the tool to rotate, producing the main cutting motion.
Feed Motion
The spindle can move arbitrarily relative to the worktable, and this kind of translation is called feed motion. Feed motion is also known as secondary cutting motion.
Mechanical Coordinates
The rectangular coordinate system fixed on the worktable, when standing facing the front of the CNC router table, the mechanical coordinate X axis points to the right, the Y axis points away from you, and the Z axis points directly up. Since the Y-axis feed is the movement of the worktable, the worktable moves in the Y- (close to itself) direction when feeding in the Y+ direction.
Workpiece Coordinates
The origin of the workpiece coordinates can be determined arbitrarily within the machine tool motion range, and the directions of the three coordinate axes are the same as the machine coordinates. NC programs usually use workpiece coordinates to determine the feed path.
G code
G code is a language that tells CNC machine tools how to make parts. It is an imperative programming language that defines the manufacturing process by telling the machine tool where to move, how fast to move, which trajectory to use, and so on.
Principle
CNC router is actually a three-dimensional computer numerical control system. Its working principle is to install special design and typesetting software in a general-purpose computer to design and typeset graphics and text, automatically generate processing path information, and transfer the tool path through a USB interface or other data transmission interface. The data is transmitted to the single-chip microcomputer, and the CNC system receives the tool path data, completes a series of functions such as display and user interaction, and uses a specific algorithm to convert the input path information into CNC information, and the controller converts the information to drive stepping motors or servos. The signal (pulse train) of the motor controls the X, Y, and Z axes of the CNC router machine to move. Simultaneous milling can engrave various 2D or 3D graphic characters designed on the computer to realize routing automation.
Types
Fundamentally speaking, there are 8 different types of CNC routers with different functions to suit the different business requirements of buyers, including:
Type 1. 3 Axis CNC Routers
3 axis CNC router moves along the X-axis, Y-axis and Z-axis at the same time. Cutting along the X-axis makes the router bit move from front to back, cutting along the Y-axis to make it move from left to right, and cutting along the Z-axis to make it upward and downward. 3 axis CNC routers are mainly designed for flatbed machining, and have functions of cutting, engraving, carving, and hollowing. They are widely used in wood carving, MDF cutting, stone engraving, family background wall, tombstone carving, aluminum cutting, blister products and more industries.
Type 2. 4th Axis CNC Routers
A 4th axis CNC router machine is to add a rotary axis on the basis of a three axis CNC router machine, which is commonly known as the fourth axis. This rotary axis CNC router machine can engrave any graphic patterns, supports scanners, and directly supports G code formats generated by UG, ArtCAM, Type3, CorelDraw, Proe and other CAD/CAM software. This machine adopts embedded DSP numerical control system or PCI control card numerical control system, which can realize the functions of continuous engraving and power-off memory, and can realize completely offline operation. This type of CNC machine is generally used to make cylindrical relief, that is, to make relief carving on the surface of the cylinder.
Type 3. 4 Axis CNC Routers
4 axis CNC router machine actually refers to X, Y, Z, and A (some people call it C, which is actually a question of how it is called). The four axes are linked, which means that the four axes can move at the same time. In addition to the basic functions of 3 axis CNC machine, the 4 axis CNC machine also has a 3D machining function. It is widely used in furniture making, cabinet door making, mold making, 180 degree swing carving and many other occasions.
Type 4, 5 Axis CNC Routers
5 axis CNC router machine has all the features of three-axis and four-axis CNC machines, and also can carry out five-axis linkage machining. It can process all-round surfaces without dead ends. It is usually used in the bending wood furniture industry. It can be used for trimming and solid wood carving. It can also be used in the mold making industry, such as car models, high-speed rail aviation models, bathroom blister plaster molds, and architectural models.
Type 5. ATC CNC Routers
ATC CNC router with automatic tool changer has an independent tool magazine, which can automatically change the required tools during the processing of the workpiece without stopping the work. When you can cut complex patterns, you can choose different tools, which greatly accelerates work efficiency and improves product quality. Automatic tool changing methods include linear ATC and disc ATC.
Type 6. Nesting CNC Routers
Nesting CNC router is mainly used to open a board into different sizes. It is a special equipment for cutting, perforating and milling in the customized panel furniture production line. It has a double-layer adsorption table and auxiliary feeding rollers to facilitate workers' access The operation is quicker and simpler. The bed structure and accessories used by the CNC nesting machine are much higher than that of the wood CNC machine, which can adapt to the long-time cutting work, and the speed is fast. The CNC cutting machine can cooperate with a variety of design and layout to optimize the cutting software, which can greatly improve the utilization rate of the plate, and the software can automatically open the order and automatically open the material, and the operation is simple to produce. The wood CNC machine can cooperate with automatic feeding, automatic unloading, automatic labeling and other automation systems to realize automatic production. One person can complete the operation and save labor; and the nesting CNC machine has more detection and fault tolerance mechanisms, operation Simple, ordinary workers can complete the operation after simple training.
Type 7. Hobby CNC Routers
Hobby CNC router is a small CNC machine for beginners with hobbyists, which is usually known as desktop CNC router machine or portable CNC router machine. A hobby CNC router is mainly used for sign making, logo making, letter cutting, mold making, and advertising.
Type 8. Industrial CNC Routers
Industrial CNC router is a large-format CNC machine for commercial use and industrial manufacturing. According to the classification of different materials and the classification of the size of the project, we can effectively choose different types of CNC router machines to complete our industrial operations. The current computer control mode can provide us with better operating effects. It is simple and can complete our different machining requirements in large quantities. It can play its greatest role in our industrial manufacturing.
Applications
CNC routers are mainly used in woodworking, arts & craft, gift making, sign making, mold making, electronics, construction, printing and packaging, advertising business, decorations, hospitals, school education, hotels, office buildings, bathing centers, and industrial manufacturing. The materials that can be cut include acrylic organic board, PVC board, hibiscus board, two-color board, wood board, MDF, marble, fireproof board, rubber board, glass, aluminum, brass, copper and more soft metals.
1. Advertising: It is used to carve and cut all kinds of signs, letter, logos, crafts, plexiglass, 3D billboards, figure statues, embossed medals, organic plate embossments, 3D door head characters;
2. Model Making: It is used for making sand table models, house models, button and embossing molds, printing and bronzing molds, injection molds, stamping molds, shoe molds;
3. Woodworking: It is used for embossed pattern design and production, which is suitable for furniture making, cabinet making, home decoration, wood crafts making, wood sign making;
4. Circuit production, drilling, slot milling in the development of new printed circuit boards;
5. Seal engraving of various fonts and materials;
6. Electrode machining of EDM machine tools;
7. Mechanical machining for dial and ruler scale;
8. Automobile industry, tire mold, car lamp mold and decoration mold machining.
Buying Guide
No matter which type of CNC router, it has its own features and advantages. Different types of CNC routers can be applied to different materials and sizes, so how do you choose a CNC router suitable for your work?
1. Pay attention to the functions. The drive motor has high power and low power. Some CNC routers with low power are only suitable for processing materials such as two-color boards, architectural models, small signs, three-dimensional crafts, etc. This technology has been popular for a while, but the power is too small and its application range is greatly affected;
2. To understand the performance and function of the drive motor, the spindle motor is also very important, because the spindle motor of the CNC carving machine is generally not covered by the warranty, and the spindle motor works continuously for a long time, a bad spindle motor will also affect the use of the CNC engraving machine;
3. Pay attention to the CNC router table tops, they are divided into two categories, one is a large-format CNC cutting machine, the table top is generally more than one meter, but the cutting accuracy of this type of machine is generally poor; the other type is a CNC cutting machine with a moderate table tops, which is generally used for fine cutting and organic sign production. When purchasing, users should choose the appropriate model according to the work they often do;
4. In addition, the adjustable range of the speed of the spindle motor, the general adjustable range of speed is several thousand to 30,000 revolutions per minute, if the speed is not adjustable or the adjustable range of speed is small, then the application range of the CNC carving machine is subject to great restrictions, because different materials must be engraved with different spindle speeds;
5. CNC controllers are generally divided into two types. One type of controller is only used for driving, and all its calculation work is completed by the computer. When the CNC carving machine is working, the computer is in a waiting state and cannot perform typesetting work; the other type of controller uses single-board computer or single-chip computer control, this type of controller is actually a computer, so as long as the CNC carving machine starts to work, the computer can immediately perform other typesetting work, especially when carving for a long time, the advantages of this model are particularly obvious. Which type to choose should be decided according to one's own economic ability and usage habits;
6. Screw rod and guide rail are also important parts of CNC engraving machine. Good screw rod and guide rail are the guarantee of the accuracy and performance of the CNC engraving machine when it is used for a long time;
7. The manufacturing process of the CNC engraving machine frame: When the high-power CNC engraving machine is working, the body must be precise and stable. Therefore, the casting body should be used for long-term high-power engraving to ensure its processing accuracy and stability. As a hobby CNC machine, there are generally no strict requirements;
8. In addition to the above configuration, you also need to pay attention to the reputation of the CNC router brand, after-sales service, whether it has its own production plant, whether it has its own R&D team, etc.
User Guide
Start
1. Turn on the power of the control computer host and monitor, and start the CNC router software;
2. Press the power switch of the CNC routing machine;
3. Turn on the cooling water pump of the spindle motor and check the flow of cooling water;
4. If you start the machine for the first time this day, press down the handle of the lubricating oil injector once to fill the lubricating part with lubricating oil;
5. Carry out the operation of returning to the machine origin in the CNC router system, and eliminate possible collisions before operation;
6. Manually make each feed axis move 1~2 back and forth within the full stroke.
Clamping
1. Place the cushion material in the center of the worktable;
2. Place the workpiece to be processed on the mat material;
3. Use at least 4 sets of pressure plates to fix the workpiece on the workbench;
4. Check whether the workpiece is clamped firmly;
5. Edge seek, set the origin of the workpiece:
5.1. Move the spindle along the feed axis that accurately sets the origin until the tool is about to touch the workpiece;
5.2. Start the spindle;
5.3. Switch to single-step movement with a step distance of 0.01mm or 0.05mm;
5.4. Move in a single step until the rotating tool touches the workpiece, and a slight noise will be heard at this time;
5.5. Reset the axis workpiece coordinate to zero or record the current machine coordinate;
5.6. Move the axis to make the tool leave the workpiece, and pay attention to confirm that the moving direction is correct.
Tool Changing
1. Disconnect the power supply of the CNC routing machine to ensure that the spindle motor stops;
2. Move the spindle to a position that is convenient for tool change, and place the soft material directly under the tool to avoid damage to the cutting edge when the tool falls;
3. Fix the spindle with a small wrench, and use a large wrench to turn the chuck nut clockwise (viewed from top to bottom), taking care not to hit the cutting edge with the wrench;
4. If you need to replace the chuck, completely unscrew the chuck nut and replace the chuck to remove the foreign matter in the chuck and the chuck nut;
5. Check whether the cutting edge of the tool to be clamped is intact;
6. Install the chuck and nut on the spindle;
7. Insert the tool to be clamped into the hole of the chuck, as far as possible according to the actual situation (but the cylindrical part of the tool cannot be inserted completely), and tighten the nut by hand. This step and the previous step cannot be reversed: do not insert the tool first and then install the nut on the spindle;
8. Tighten the nut with two wrenches, be careful not to apply too much force, and also be careful not to hit the cutting edge with the wrench;
9. Confirm that the wrench is away from the spindle and turn on the power of the CNC routing machine;
10. Re-calibrate the tool and set the Z coordinate of the workpiece origin.
CNC Programming
1. Confirm the following tasks:
1.1. The tool is firmly clamped;
1.2. The workpiece origin is set correctly, especially the Z coordinate of the workpiece origin after tool change;
1.3. The workpiece is clamped firmly;
1.4. The CNC program is loaded correctly.
2. Adjust the feedrate override to about 30% in the CNC router system, and start the CNC program;
3. After confirming that there is no abnormality in the operation, adjust the feedrate override to the normal value;
4. There must be someone on duty during operation.
Shut Down
1. Back to the machine origin;
2. Remove the tool and allow the chuck nut to stay on the spindle;
3. Turn off the CNC routing machine;
4. Turn off the computer. This step cannot be reversed from the previous step.
Troubleshooting
Alarm Failure.
Over-travel alarm indicates that the CNC cutting machine has reached the limit position during operation. Please check according to the following steps:
1. Whether the designed graphic size exceeds the processing range;
2. Check whether the connecting wire between the machine motor shaft and the lead screw is loose, if so, please tighten the screws;
3. Whether the machine and the computer are properly grounded;
4. Whether the current coordinate value exceeds the value range of the software limit.
Overtravel Alarm & Release.
1. When overtravel, all motion axes are automatically set in the jog state, as long as you keep pressing the manual direction key, when the machine leaves the limit position (that is, the overtravel point switch), the connected motion state will be restored at any time;
2. Pay attention to the direction of movement when moving the workbench and keep it away from the extreme position;
3. The soft limit alarm needs to be cleared to XYZ in the coordinate setting.
Non-Alarm Fault.
1. If the repetitive machining accuracy is not enough, check according to the second item of the first tip;
2. When the computer is running and the machine does not move, check whether the connection between the computer control card and the electrical box is loose, if so, insert it tightly and tighten the fixing screws;
3. When the machine cannot find the signal when returning to the machine origin, check according to the second tip. The proximity switch at the machine origin is malfunctioning.
Output Fault.
1. No output, please check whether the computer and the control box are well connected;
2. Check whether the space in the settings of the engraving manager is full, delete unused files in the manager;
3. Whether the wiring of the signal wire is loose, carefully check whether the wires are connected.
Machining Failure.
1. Whether the screws of each part are loose;
2. Check whether the path processed by yourself is correct;
3. Whether the file is too large, causing computer processing errors;
4. Increase or decrease the spindle speed to adapt to different materials (usually 8000-24000);
5. Loosen the chuck of the router bit, turn the bit in one direction and clamp it, and place the bit upright, so as to avoid the machining project is not smooth
6. Check whether the tool is damaged, replace it with a new one, and re-engrave.
Summary
From this article, you'll have an idea on what is a CNC router? how does it work? how many types? what is it used for? how to use? how to buy or DIY a CNC router machine for hobbyists or commercial use. It is the ultimate guide to beginners.